Ampd Energy’s Energy Storage Systems (ESS) Enable More Efficient Job Site Power
.avif)
Background
The City of Las Vegas contracted LGA Architects, along with the design firm BNIM and landscape architecture company OJB, to design a new downtown civic center building and plaza. This integrated project, commonly called the Las Vegas Civic Center (LVCC), covered two city blocks and was designed to support the net zero energy and carbon reduction goals of the city’s 2050 Master Plan. When completed, the facility would feature a park and two large buildings with multiple terraces, including an overhead canopy supporting a photovoltaic array.
The job site required two large tower cranes and two construction elevators, which were provided by the UPERIO Group and Compass Equipment.
Introduction & Project Information
The Challenge
The construction site was located in the heart of downtown Las Vegas, a historic area with an older power grid. Despite being in a busy urban neighborhood, the job site had limited access to power. As a result, the contractor considered using diesel-powered crawler cranes, which provide less visibility because they are operated from the ground. However, this less efficient solution was likely to slow the project’s timeline and increase operational costs.
Uperio and Compass proposed using electric tower cranes, which would provide superior performance to the crawler cranes. During the early stages of the project, UPERIO and Compass used two massive 400 kVA generators to power the two tower cranes. These expensive machines required a large footprint and consumed a lot of diesel fuel.
Further, the crew had to improvise strategies to make the generators work hard enough to supply the required power reliably, eventually adding unnecessary electric heaters to provide artificial electrical load on the generators between lifts. Two additional 120 kVA generators would be needed to power the construction elevators.
The Solution
UPERIO and Compass partnered with Ampd Energy to supply two Enertainer™ energy storage system (ESS) units, which were used to power all four pieces of hoist equipment. This enabled them to provide the client with a turnkey package that delivered a more reliable, economical, and sustainable power supply than the noisy, fuel-hungry generators.
The Ampd Enertainer is the first battery ESS designed specifically for the needs of the construction industry. By reducing or replacing the need for generators, the unit makes construction sites quieter, safer, and more efficient while dramatically reducing or eliminating diesel-related air pollution. It also has a footprint about half the size of a comparable generator.
Once the Ampd Enertainers were installed, the team was able to significantly downsize to a pair of 70 kVA supply generators, one for each ESS, dramatically reducing the site’s fuel consumption and carbon footprint. The onboard computers in the Ampd units automatically managed the capacity and run times of these generators, switching them on and off as needed to optimize battery charging and fuel consumption.
This arrangement enabled the ESS units to supply all the power needed for the tower cranes and construction elevators, which were operated for up to two shifts each working day.
Results
Using Ampd Enertainers reduced the size of the on-site generators by nearly a factor of six. During the five-month deployment, this saved the job nearly 9,000 gallons of diesel fuel and reduced its carbon emissions by close to 45 tonnes of carbon. The site was also quieter because the supply generators only needed to run a few hours each day.
The crew enjoyed more reliable power while dramatically reducing generator maintenance costs and downtime. In addition, the solution eliminated many logistical issues by minimizing the number of fuel truck visits needed in a congested urban area.
By leveraging the greater efficiencies of tower cranes, the crew was able to complete the project about two months ahead of schedule.
“We were able to supply a more efficient tower crane, not only from a cost perspective but from an environmental perspective. It also contributed to finishing the job earlier,” said Kelly Hadland, president of Compass Equipment. “We plan on using these again in the future. They expand our ability to put tower cranes on more projects where it’s too expensive or restrictive to use a big generator. We hope to expand the presence of this product and make a difference in the industry,” he added.
Download Case Study
Discover how our Enertainers can enhance efficiency while protecting the environment and reducing costs.
.avif)
Download Case Study
Discover how our Enertainers can enhance efficiency while protecting the environment and reducing costs.
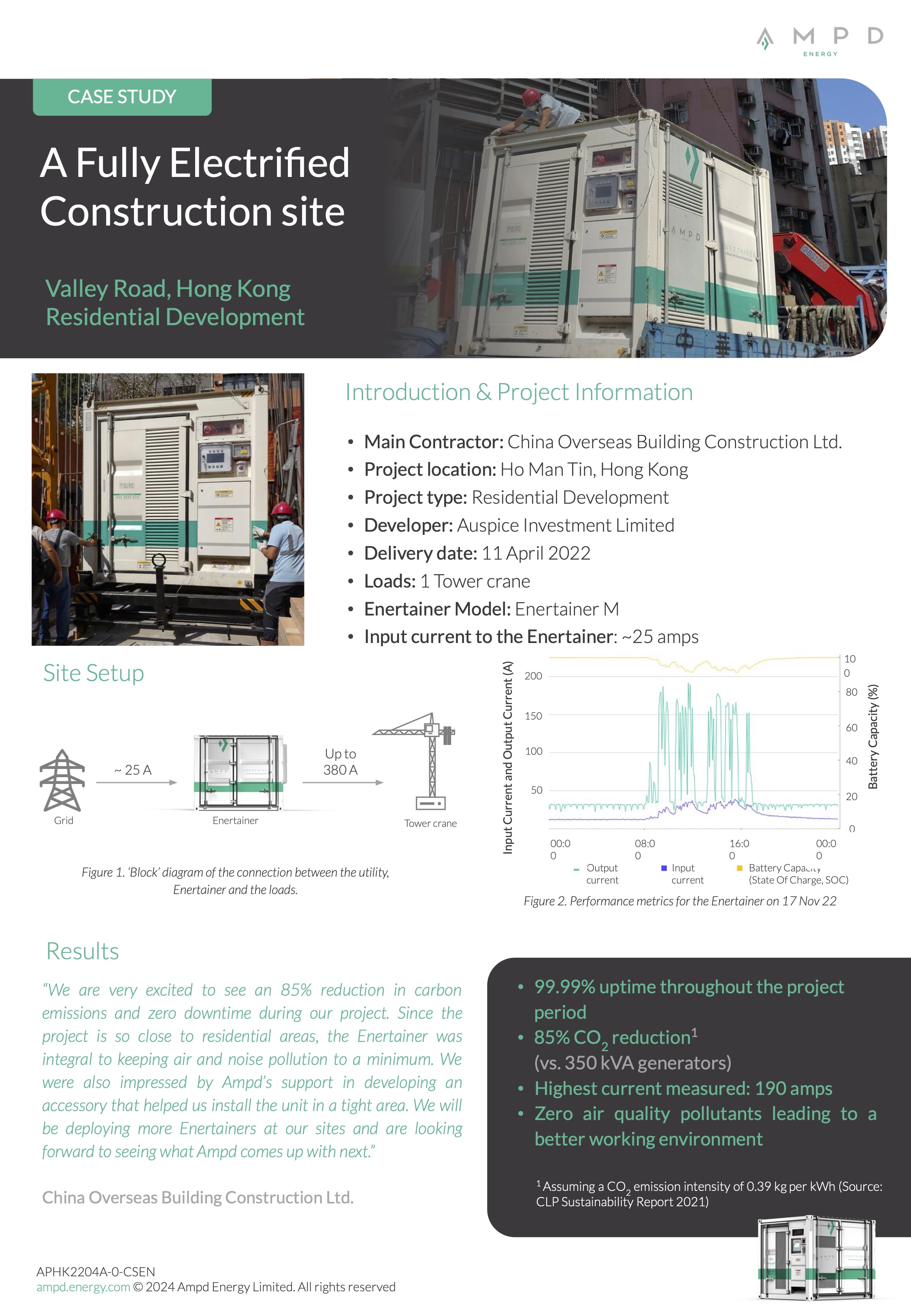